1. EXPERIENCE
Naturally, you want to engage an experienced supplier. When you start your search, research their credentials in a variety of areas:
- How many years have they been in business? Modular data centers have been around for more than a decade, but that doesn’t mean you need to look for a company that has been building data centers for the last 10 years. Look at their overall experience. Do they have the expertise to advise you about your modular data center needs? Ask about their professional staff, especially their engineering team, and see if they have the experience you want. Also, be sure that their certifications are current and they have kept up with industry best practices. You want to find a supplier with a strong track record, but also one that has kept pace with the latest technologies.
- What types of data center design projects have you completed? There are different types of modular data centers, and you want to find a supplier that is well-versed in various design strategies. There are three basic modular design approaches: an ISO container data center, skid-mounted data centers and customized enclosures. As the old saying goes, “to a hammer, everything looks like a nail.” If you choose a vendor that specializes in ISO containers, then that is likely what you will get, even if another approach might be more viable. You want to be sure your supplier has the versatility and expertise to make informed recommendations and deliver the right type of data center solution.
- Do you have customer references and exemplary installations? In addition to experience and expertise, you want to look for a track record of success, and customer satisfaction is one of the best barometers. Ask for customer referrals. Ask for examples of successful past projects, including how they measured success. You also want to ask about past failures or issues to see how the vendor overcomes challenges and how they learn from past mistakes. Developing a modular data center is a collaborative process, and you want to be comfortable with your supplier’s candor and honesty, as well as their expertise.
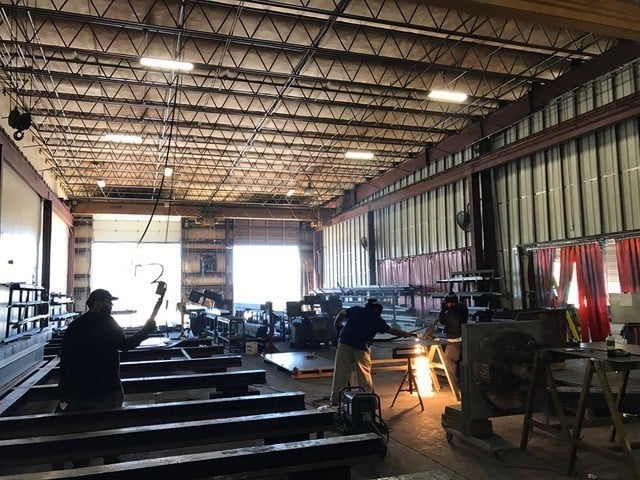
2. CUSTOMIZATION AND ADAPTABILITY
You also want to quiz them about customization and design adaptability. Even though they are delivered as completed units, modular data centers are not cookiecutter designs. On the contrary, they are highly customized and should be created to suit your unique specifications.
Assess the supplier’s data center design expertise and how they work with clients. Do they have a collaborative process in place to develop and review design criteria? Is the interaction to develop the customized data center design more than an exchange of information, but also a mutual learning experience? Ideally you want to feel confident in the vendor’s expertise and counsel, but you also want to be sure they understand your unique needs and concerns.
In addition to working with you as the customer, the modular data center vendor has to work with everyone else in the value chain. Do they have a collaborative process to work with your engineers and on-site contractors? The last thing you want is to have your engineering firm, your general contractor and your modular data center contractor at odds due to lack of communication or an inability to work together.
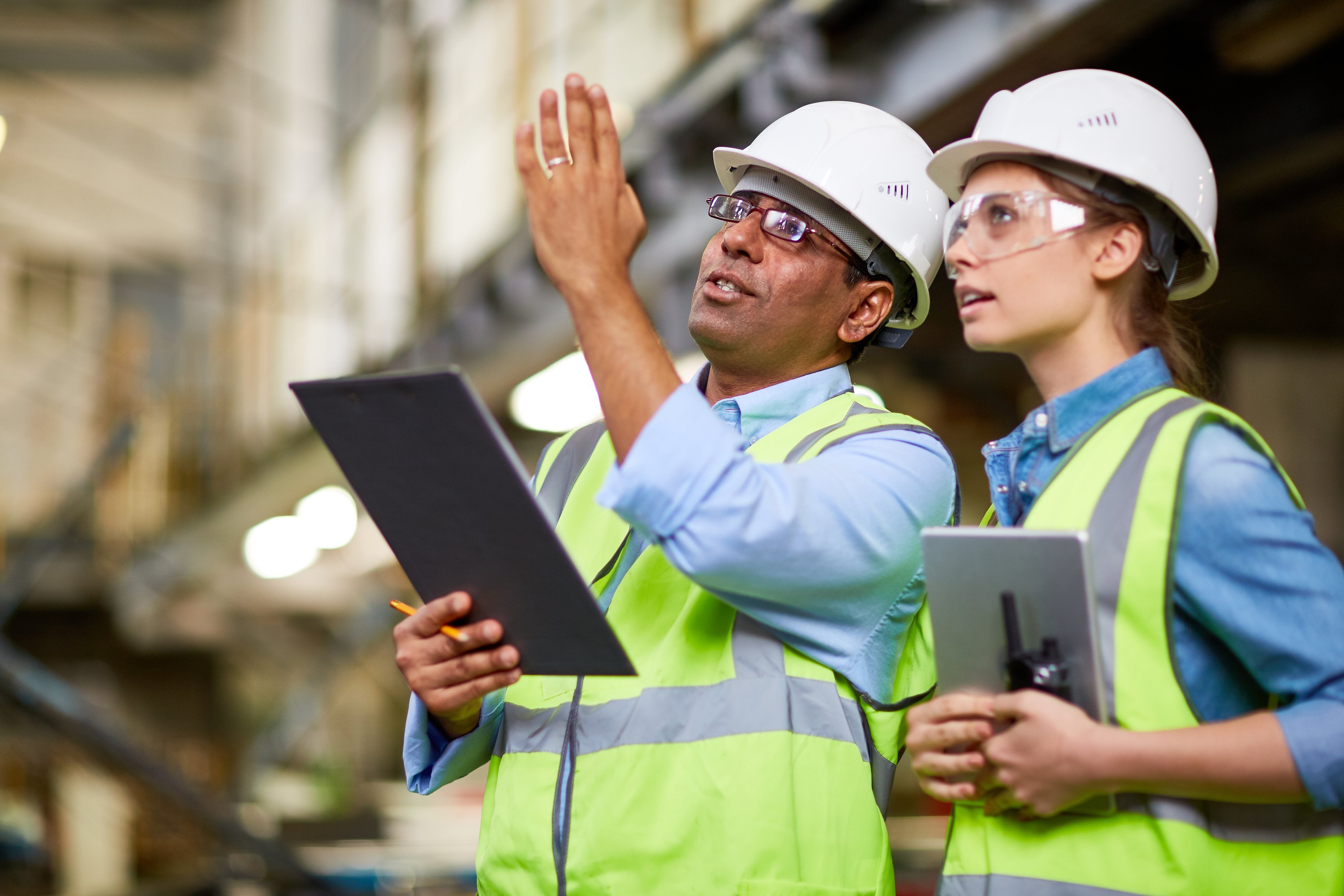
Also determine if the supplier is prepared to make your contract a priority. You want to be sure that modular data center design is a primary part of their business and not just a secondary offering, as this will determine if you get their full attention. You also want to be sure that your contract won’t be eclipsed if a larger contract comes in the door. It’s not unheard of for an agreement to be reached to move forward, and the contract is cancelled at the last minute because a bigger job took precedence.
When discussing design and installation options, also make sure that the modular provider is both vendor agnostic or vendor neutral, and “electrical contractor agnostic.” They should be prepared to use any standardized parts, including servers and hardware that you may want to supply yourself. They also should deliver a finished data center module that complies with recognized industry standards and can be installed by a licensed electrical contractor.
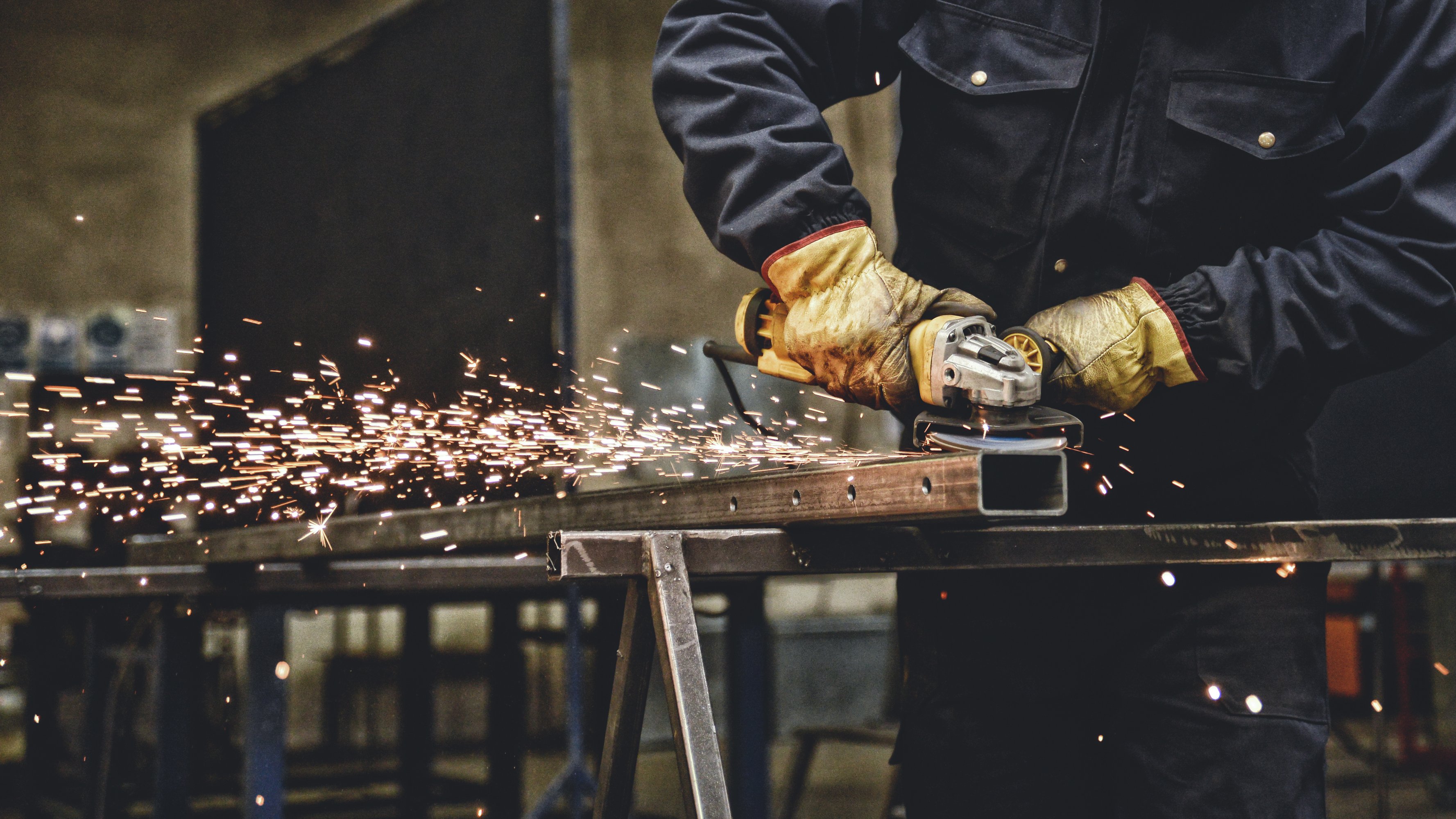
3. QUALITY ASSURANCE
Maintaining the highest quality standards throughout the design and manufacturing process needs to be a priority. Make sure to ask about specific quality assurance (QA), inspections and other procedures. And be sure to drill down into specific areas that have a direct impact on QA.
Any modular data center manufacturer should be current on all the latest safety and construction certifications.
Be sure to ask about the relevant industry standards, such as:
ISO 9001:2015 – Requirements for ISO 9001:2015 are designed to ensure that an adequate quality management system is in place. The standard was set up to demonstrate consistent quality in products and services, and to ensure conformity and ongoing improvement to production systems that improve customer satisfaction.
Underwriters Laboratories (UL/cUL) – Underwriters Laboratories (or cUL in Canada) are accredited by the American National Standards Institute (ANSI) and the Standards Council of Canada (SCC) and is dedicated to applying scientific research to improve safety and address risks. Among other areas, UL is responsible for developing standards for safety performance and sustainability, including requirements to minimize risk and injury. These safety standards are designed to protect both end users and manufacturers.

QRXA – Listed as a subcategory in UL, QRXA covers installation of wiring and electrical systems in prefabricated structures, such as modular data centers.
ETL Listing – Administered by Intertek, the ETL Listed Mark is proof of compliance with North American safety standards and extends to manufacturing services and processes, as well as products.
CSA Group – The CSA Group is a worldwide group that develops tests, safety inspection and certification protocols for manufacturing to demonstrate that products are safe and in compliance with environmental and performance operating standards.
American Welding Society – For enclosures and construction that requires welding, The American Welding Society (AWS) maintains standards designed to promote safety and health, while ensuring qualified welders deliver reliable finished products.
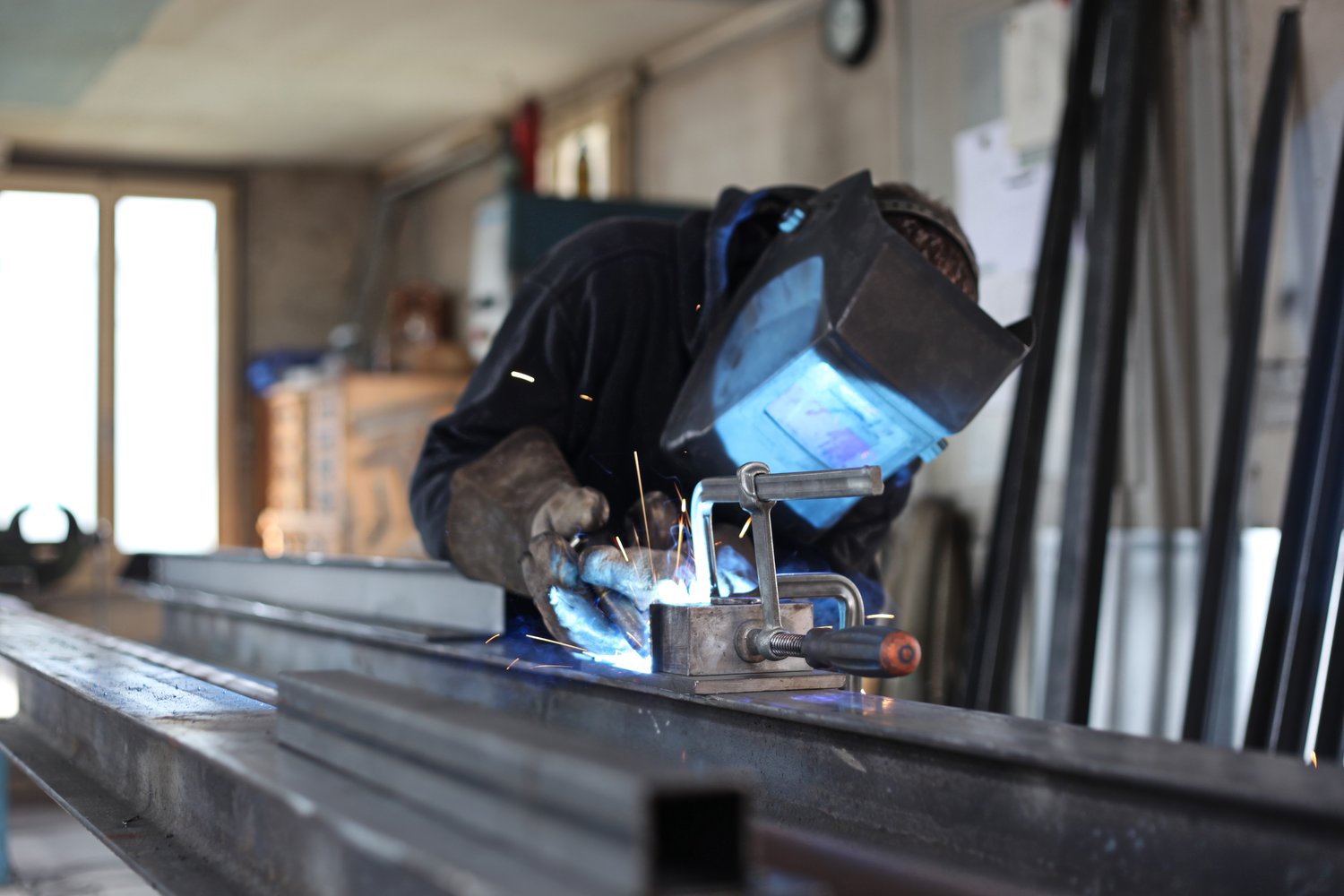
There are additional safety regulations as well, but compliance with these well-known standards will demonstrate that your vendor is serious about safety, including delivering a safe end product.
In addition to safety, you want to ask about QA certifications and test procedures. Do they test to the standards set by the InterNational Electrical Testing Association (NETA)? Part of ANSI, the NETA is responsible for third-party electrical testing, and an independent firm should perform NETA Breaker Testing and Commissioning. Although you may not want to pay for third-party testing, your supplier should perform their own testing and be confident that they will meet NETA standards.
Also, be sure to inquire about environmental impact inspections, such as testing for rain penetration, which is a standardized test maintained by the American Society for Testing and Materials (ASTM). As part of final product testing, you also want to be sure to have access to Factory Acceptance Testing (FAT) or factory witness testing for on-site examination and testing of cables, cooling, power, fire suppression and other systems prior to shipment.
Asking for quality assurance testing and compliance is a good place to start, but you also want to be sure there is a comprehensive quality control plan in place that includes corrective action. If there is a problem with a design issue, e.g., engineering changes or retrofits, then there needs to be a procedure to identify those issues and correct them. The same is true for process concerns, such as welding.
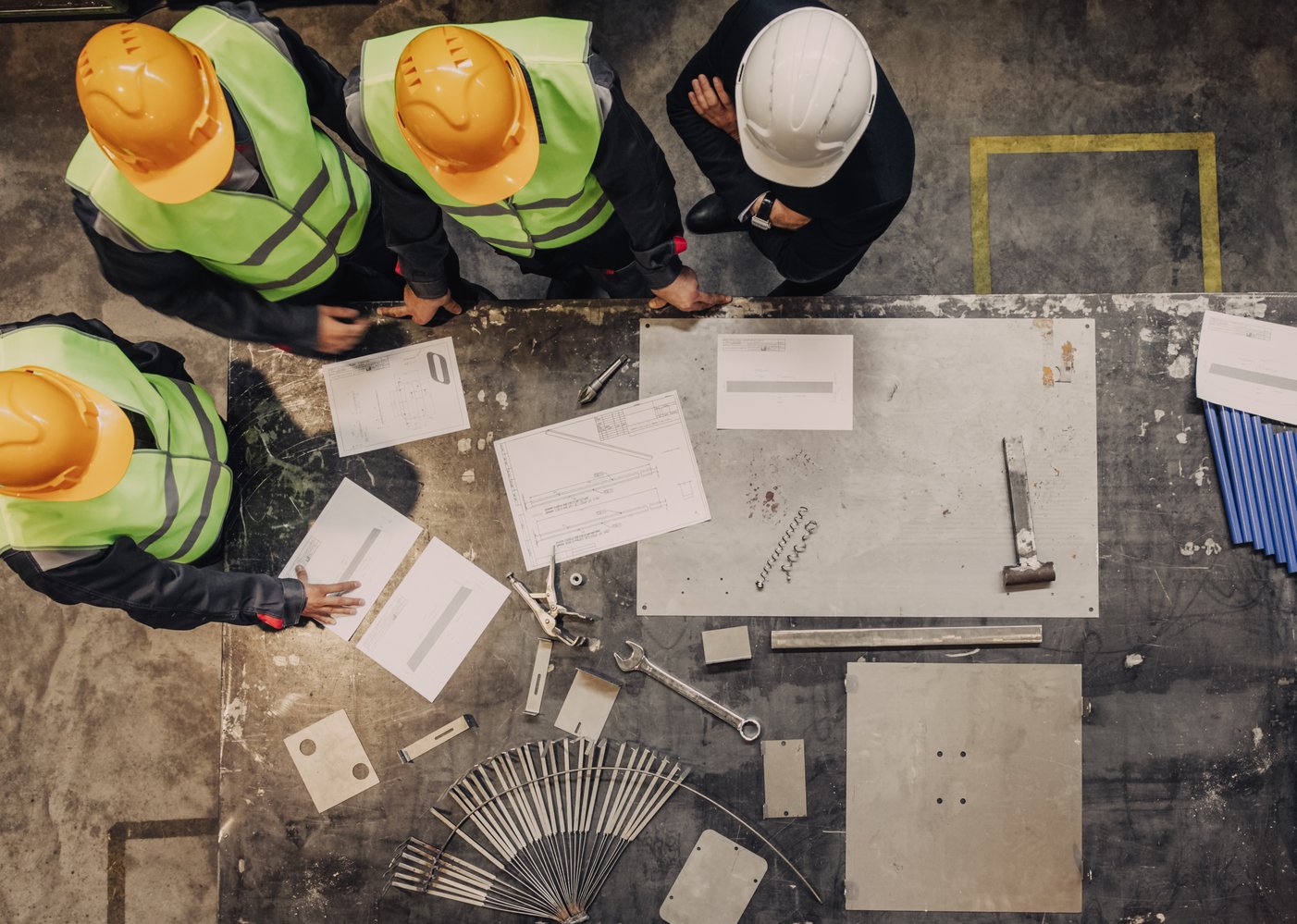
4. ADDITIONAL CONSIDERATIONS
In addition to standards compliance, be sure to ask about other manufacturing procedures and processes that have an impact on efficiency and time to delivery.
For example: Where are materials sourced, and will access to components impact production time? You want to make sure that your supplier has a store of components and reliable suppliers who can deliver on time to keep the production schedule on track.
Is their primary business dedicated to manufacturing modular data centers? Your greatest concern should be that you will get the attention you deserve in design and production, which will ensure delivery dates will be met. You don’t want delays because resources are needed elsewhere or because another more lucrative project could affect your contract.
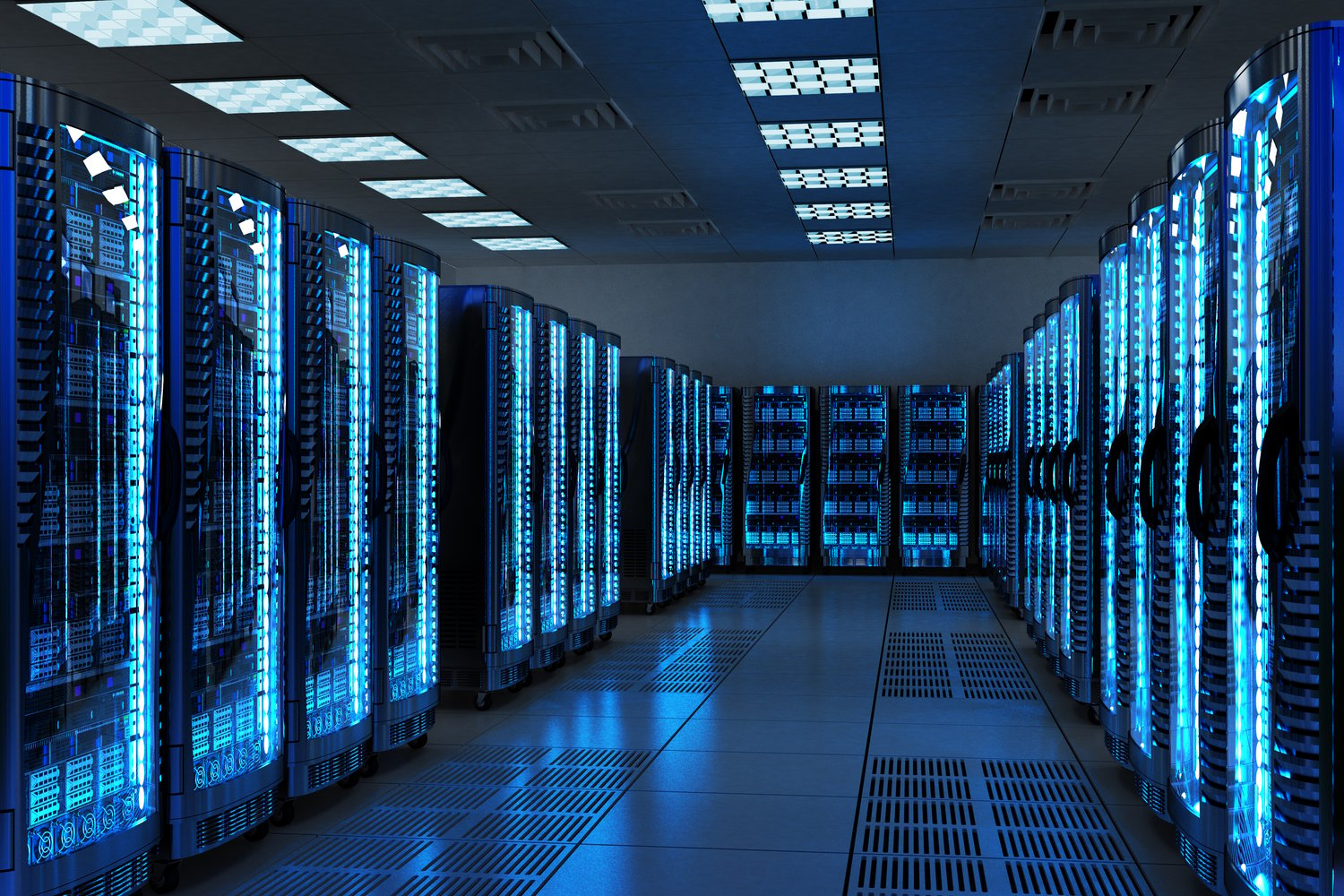
Also inquire about active project management. Every business has some form of project management infrastructure in place. You want to be sure that, as a client, you have a single point of contact who tracks every aspect of your project and who can serve as a liaison to eliminate roadblocks. You want to be sure there is a representative actively managing your contract and that there is continuity, so there aren’t changes in responsibility that can cause confusion and delays.
Also, be sure to get details about delivery procedures. Some suppliers just deliver the finished data center and consider the project done. Others include on-site support to assist with data center installation and troubleshooting. Those that offer these services are the best partners, as they go above and beyond to understand your business goals and objectives. They use this knowledge to help you address any issues before they become a problem and ensure your data center is going to offer all the benefits that it was designed to. Be sure to ask about support during and after the installation process, including availability of 24-hour support in conjunction with delivery and post-delivery support procedures.